There are several different types of field tests that can be performed at the time of drilling. For exam-ple, the SPT consists of driving a thick-walled sampler in order to determine the driving resistance
of the soil (see Fig. 2.10).
Test Procedure. The SPT can be used for all types of soil, but in general, the SPT is most often
used for sand deposits.
The SPT can be especially of value for clean sand deposits where the sand falls or flows out from the sampler when retrieved from the ground.
Without a soil sample, other types of tests, such as the SPT, must be used to assess the engineering properties of the sand.
Often when drilling a borehole, if subsurface conditions indicate a sand strata and sampling tubes come up empty, the sampling gear can be quickly changed to perform SPT.
The system to drive the SPT sampler into the soil, known as the drive-weight assembly, basically
consists of:
- the hammer
- hammer fall guide
- anvil
- and a hammer release system
Hammer. The metal hammer is successively lifted and dropped in order to provide the energy that
drives the SPT sampler into the ground.
Hammer Fall Guide. This part of the drive-weight assembly is used to guide the fall of the hammer as it strikes the anvil.
Anvil. This is the portion of the drive-weight assembly which the hammer strikes and through
which the hammer energy is passed into the drill rods.
Hammer Release System. This is the part of the drive-weight assembly by which the operator lifts
and drops the hammer. Two types of systems are commonly utilized, as follows:
1.The first hammer release system is the trip, automatic, or semiautomatic system, where the ham-mer is lifted and allowed to drop unimpeded.
2.The second hammer release system is commonly referred to as the cathead release system. It is a
method of raising and dropping the hammer that uses a rope slung through a center crown sleeve
or pulley on the drill rig mast and turns on a cathead to lift the hammer.
The cathead is defined as a spinning sleeve or rotating drum around which the drill rig operator wraps the rope used to lift and drop the hammer by successively tightening and loosening the rope turns around the drum.
The drill rig operator should use two rope turns on the cathead when lifting the hammer because more than two rope turns on the cathead impedes the fall of the hammer
![]() |
SPT procedure |
There are many different types of hammers utilized for the SPT.
A commonly used hammer type is the safety hammer, which is defined as a drive-weight assembly consisting of a
- center guide rod
- internal anvil
- and hammer that encloses the hammer-anvil contact.
Typical internal designs of safety hammers are shown in ASTM D 6066-96 (2004).
Per ASTM D 1586-11, “Standard Test Method for Penetration Test and Split-Barrel Sampling
of Soils,” sampler dimensions and test parameters for the SPT must be as follows:
• Sampler inside tube diameter =1.5 in. (3.81 cm), see Fig. 2
• Sampler outside tube diameter =2.0 in. (5.08 cm), see Fig. 2
• Sampler is driven by a metal drop hammer that has a weight of 140 lb. (63.5 kg) and a free-fall dis-tance of 30 in. (0.76 m)
• Sampler is driven a total of 18 in. (45 cm), with the number of blows recorded for each 6 in. (15 cm)
interval
The measured N value (blows per ft) is defined as the penetration resistance, which equals the
sum of the number of blows needed to drive the SPT sampler over the depth interval of 6 to 18 in. (15 to 45 cm).
The reason the number of blows required to drive the SPT sampler for the first 6 in.
(15 cm) is not included in the Nvalue is because the drilling process often disturbs the soil at the
bottom of the borehole and the readings from 6 to 18 in. (15 to 45 cm) are believed to be more rep-resentative of the in situ penetration resistance of the sand.
- It is desirable to apply hammer blows at a rate of about 20 to 40 blows per min.
- After performing the SPT, the minimum recommended borehole cleanout is 1 ft (0.3 m).
Thus, since the SPT itself requires 1.5 ft (0.46 m) of penetration, the minimum vertical spacing between tests is 2.5 ft (0.76 m).
Often a larger vertical spacing of 3 to 5 ft (0.9 to 1.5 m) is used between each SPT.
![]() |
SPT procedure |
Factors that Can Affect the SPT
The measured Nvalue can be influenced by the type of soil, such as the amount of fines and gravel size particles in the soil.
Saturated sands that contain appreciable fine soil particles, such as silty or clayey sands, could give abnormally high Nvalues if they have a tendency to dilate or abnormally low Nvalues if they have a tendency to contract during the undrained shear conditions associated with driving the SPT sampler.
Gravel size particles increase the driving resistance (hence increased Nvalue) by becoming stuck in the SPT sampler tip or barrel.
A factor that could influence the measured Nvalue is groundwater.
It is important to maintain a level of water in the borehole at or above the in situ groundwater level.
This is to prevent groundwater from rushing into the bottom of the borehole, which could loosen the sand and result in low measured Nvalues.
Besides soil and groundwater conditions described earlier, there are many different testing factors
that can influence the accuracy of the SPT readings (see Table 2.5).
For example, the hammer efficiency, borehole diameter, and the rod lengths could influence the measured Nvalue.
The following equation is used to compensate for these testing factors by multiplying together four factors as follows (Skempton, 1986):
The theoretical energy that should be delivered to the top of the anvil is 350 ft-lb of energy (i.e.,
140 lb times 30 in. drop).
However, the SPT theory has evolved around the concept that about 60 percent of the hammer energy should be delivered to the drill rods, with the rest being dissipated through friction and hammer rebound.
Using the cathead release system and a safety hammer will deliver about 60 percent (i.e., Em = 60) of the hammer energy to the drill rods.
Note in Eq. 2.4 that if Em = 60, no correction is required to the Nvalue for hammer efficiency.
Studies have shown that the cathead release system and a donut hammer can impart only 45 percent of the theoretical energy to the drill rods (i.e., Em = 45).
At the other extreme are automatic systems that lift the hammer and allow it to drop unimpeded and deliver higher energy to the drill rods with values of Em as high as 95 percent being reported (ASTM D 6066-96, 2004).
For other types of release systems and hammers, values of Em should be based on manufacturer specifications or pre-viously published measurements.
Even with this hammer energy uncertainty, the SPT is still probably the most widely used field
test in the United States. This is because:
- it is relatively easy to use,
- the test is economical as compared to other types of field testing,
- and the SPT equipment can be quickly adapted and included as part of almost any type of drilling rig.
The (N1)60 value (blows per foot) can also be used as a guide in determining the density condition of a clean sand deposit (see Table 2.6).
Note that this correlation is very approximate and the boundaries between different density conditions are not as distinct as implied by Table 2.6.
If(N1)60 =2 or less, then the sand should be considered to be very loose and could be subjected to significant settlement due to the weight of a structure or due to earthquake shaking.
On the otherhand, if (N1)60 =35 or more, then the sand is considered to be in a very dense condition and would be able to support high foundation loads and would be resistant to settlement from earthquake shaking.
For further details on determining the (N1)60 value for use in liquefaction studies, see ASTM D
6066-96 (2004), “Standard Practice for Determining the Normalized Penetration Resistance of
Sands for Evaluation of Liquefaction Potential.”
SUMMING UP:
A common soils test is the standard penetration test (SPT), which is performed in situ as part of the drilling and sampling operation. (The term“in situ”is synonymous with“in place.”)
The SPT measures resistance to the penetration of a standard split-spoon sampler that is driven by a 140 lbm (63.5 kg) hammer dropped from a height of 30 in (0.76 m).
The number of blows required to drive the sampler a distance of 12 in (0.305 m) after an initial penetration of 6 in (0.15 m) is referred to as theN-value or standard penetration resistance in blows
per foot.
The measured value of N is inconsistent from operator to operator because different drill rig systems deliver energy input that deviates from the theoretical value.
Therefore, the N-value obtained in the field is converted to a standardized N-value, N'.
In addition, because the N-value is sensitive to overburden pressure, corrections are applied to reference the value to a standard overburden stress, usually 2000 lbf/ft2 (95.76 kPa).
TheN-value has been correlated with many other mechanical properties, including shear modulus, unconfined compressive strength, angle of internal friction, and relative density. The correlations work best with cohesionless soils.
Table 35.9 relates N to the relative density and friction angle.


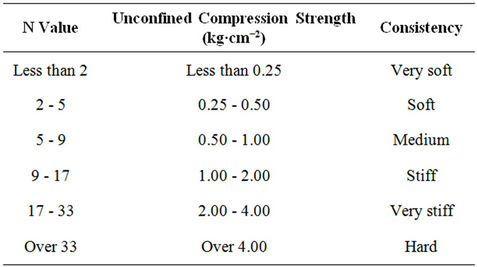

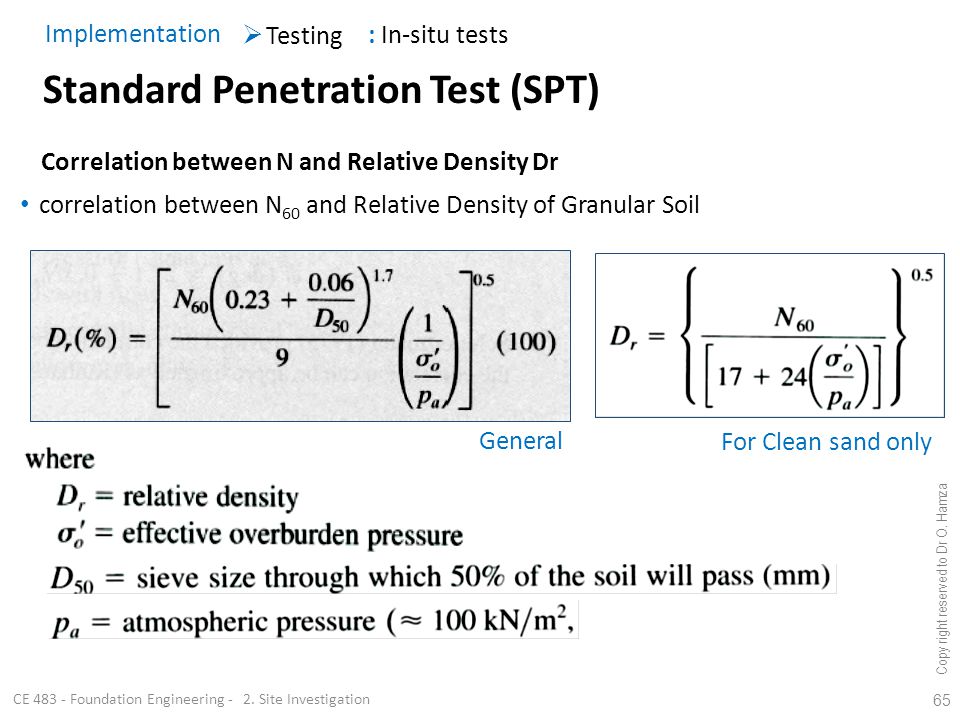
